
Login or create an account
CloseReturning Customer
I am a returning customer
Login or create an account
CloseRegister Account
If you already have an account with us, please login at the login form.
Your Account Has Been Created!
Thank you for registering with Cangzhou Xintai Cable Co., Ltd!
You will be notified by e-mail once your account has been activated by the store owner.
If you have ANY questions about the operation of this online shop, please contact the store owner.
Account Logout
You have been logged off your account. It is now safe to leave the computer.
Your shopping cart has been saved, the items inside it will be restored whenever you log back into your account.
How to control the quality of cables?
07/10/2017 | Plazathemes
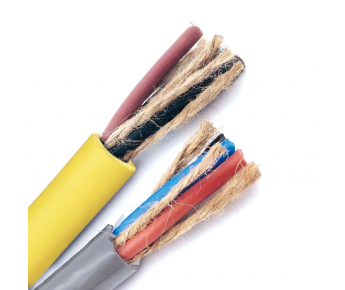
For every enterprise, product control is a crucial issue. Only by strictly controlling quality can enterprises produce high-quality products and bring economic and social benefits to the enterprise. However, quality control is not an easy task. Quality control is systematic, standardized, and procedural, which is where the competitiveness of enterprises lies. Xintai Cable has summarized six suggestions for quality control based on its own experience:
1. Do not easily determine the process, and do not change the determined process easily
1) Identify the root cause, main factors, or main manifestations of product quality issues;
2) Before clarifying the problem, the easily changeable process actually conceals the true cause and problem.
2. Process control should have a strong awareness of quantification and traceability
Quality depends on many factors. Do not overlook any details;
2) Use data to control and record any details as much as possible;
3) Inadequate control and tracking of process details can mislead the development of corrective and preventive measures.
3. You must patiently solve the problem
1) Don't be impetuous, hope to eat fat in one breath;
2) Do not ignore abnormal situations, as they are unrelated to the problem being solved.
3) Not taking action when the reasons and patterns cannot be found, and controlling and regulating the analyzed influencing factors;
4) Reviewing and reviewing past experiments and summarizing experiences and patterns;
5) Once some experience and rules are discovered, delve into them and transform them into theories. Even more waste is worth it.
You should know that 'a thousand mile embankment was destroyed by an ant nest', and you should also know 'Foolish Old Man Moves Mountains'.
Submersible pump cable. png
4. Develop a preventive mindset
1) The key to quality management is prevention, not remediation of problems;
2) Any quality issue must have symptoms to appear, depending on whether you have methods, means, and experience to monitor and identify it;
3) Pay attention to the situation where the same quality issue occurs again;
4) Use certain tools to organize daily processes and result data, discover patterns and trends from the organized results, and continuously revise them;
5) Before product processing, all control elements should be as consistent as possible.
5. Quality control must have management thinking
1) Do not rely directly on technical personnel to achieve stable product quality;
2) Product quality is manufactured, without direct management by the manufacturer, quality will never be stable;
3) Therefore, it is necessary to observe, pay attention to, and study the performance and status of the direct manufacturer of the product, and manage and transfer these performance and status;
4) If the performance and condition of the product are not controlled directly by the manufacturer, once a quality problem occurs, it is necessary to analyze the inaccurate reasons;
5) Don't think that if all the process control requirements specified in our process regulations are met, the product quality is not a problem;
6) Therefore, our process control needs to be continuously improved, and we also need to do a good job in personnel management.
6. Listen to opinions and suggestions
1) Don't think that if a person doesn't understand reality and can't solve problems immediately, their opinions are worthless;
2) But they, especially direct producers, can give us a lot of tips and reminders;
If you can solve this problem, don't listen to anyone. But when it's not possible, it's recommended to listen to others' opinions and suggestions, try and experiment, whether you like it or not;
4) Quality management thinking often touches on the forefront of technology. Even a casual comment or complaint can point out or imply a significant technological innovation, so professionals should be detail oriented and attentive individuals